WELCOME TO
IMPROVEMENT DIRECT
Lean Business Coaching & Consulting
Get the help you want to make the improvements you need

Improvement Direct helps you:
Identify and focus on your priorities for improvement: Make the right choices toward maximum gains. Amplify your improvement efforts through agile group engagement methods. Get results through Lean Management: Better delivery of services and products, a safer & healthier work-place, a happier motivated Team, improving planet footprint and sustained profits & growth.
We offer valuable support to do this…. just enough of the right stuff... because it’s so essential that you control the Lean implementation process and fully own the learning, the methods and the outcomes.

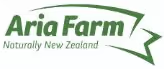
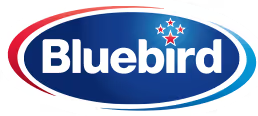
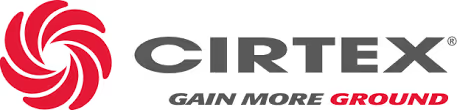

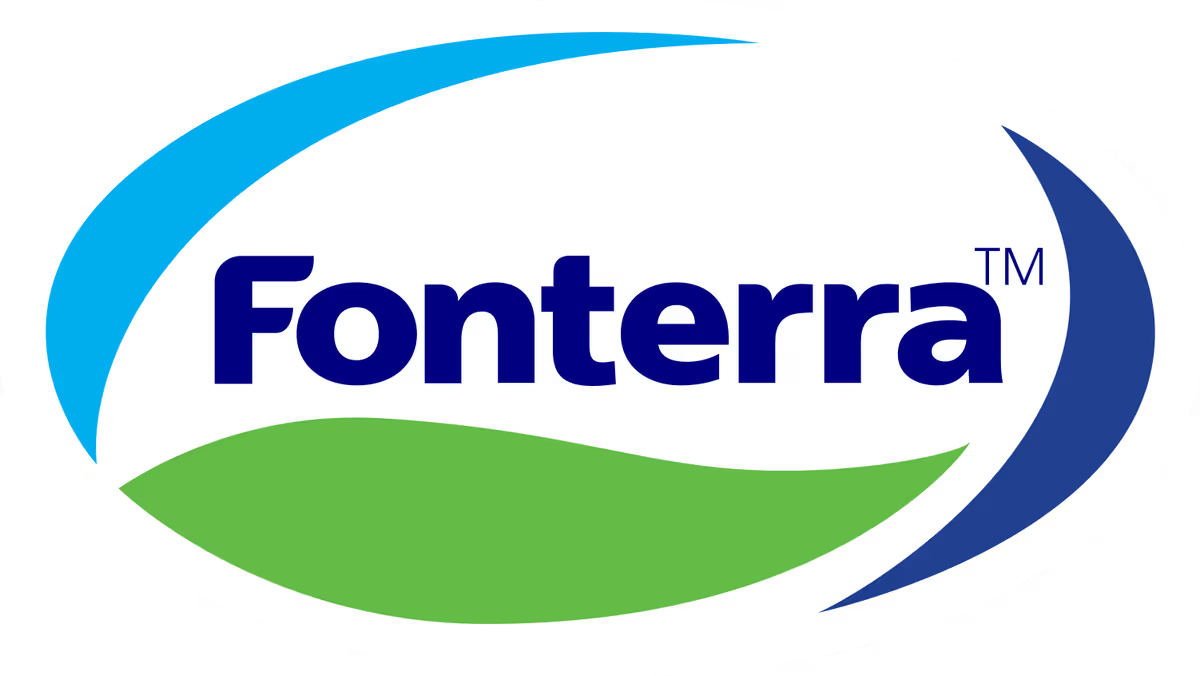
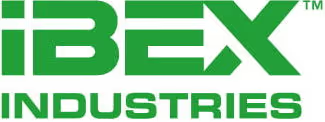
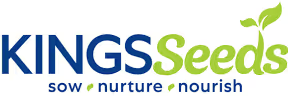
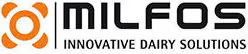
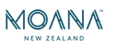
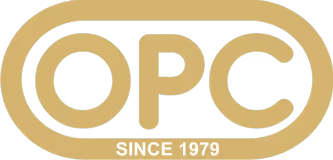
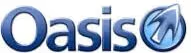
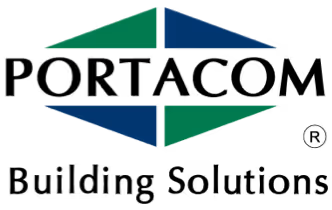
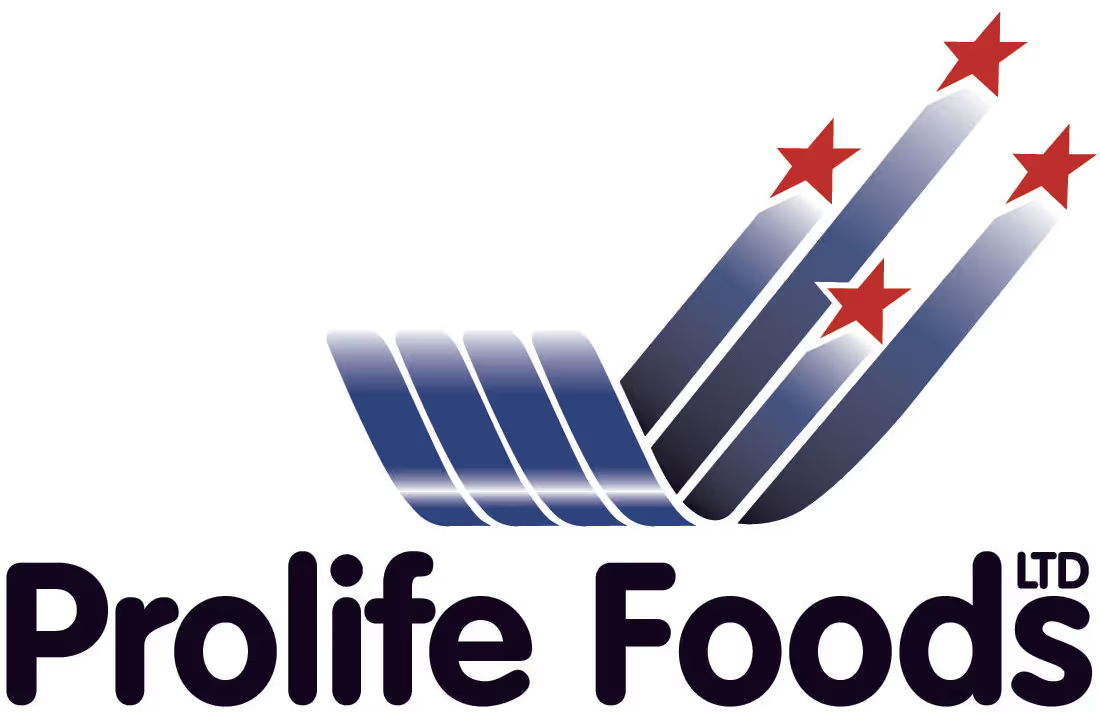
.png)
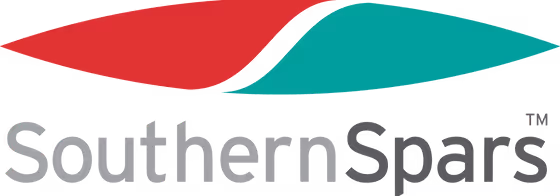
.svg.avif)

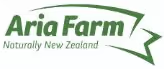
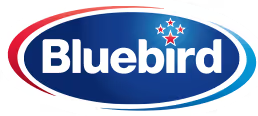
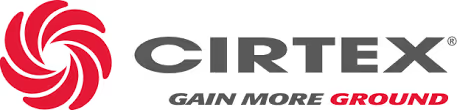

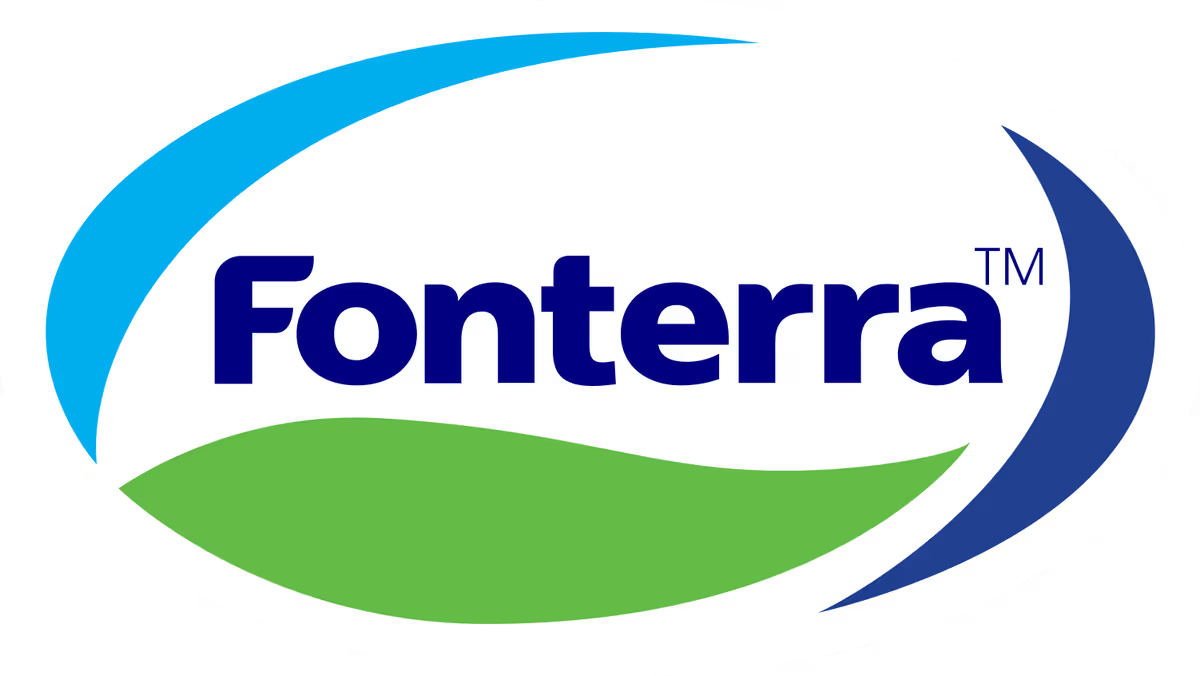
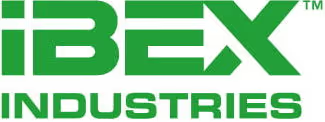
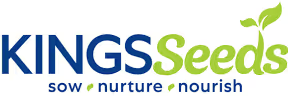
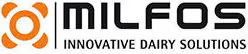
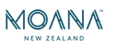
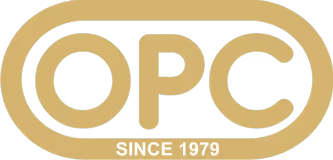
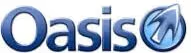
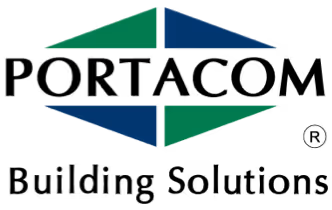
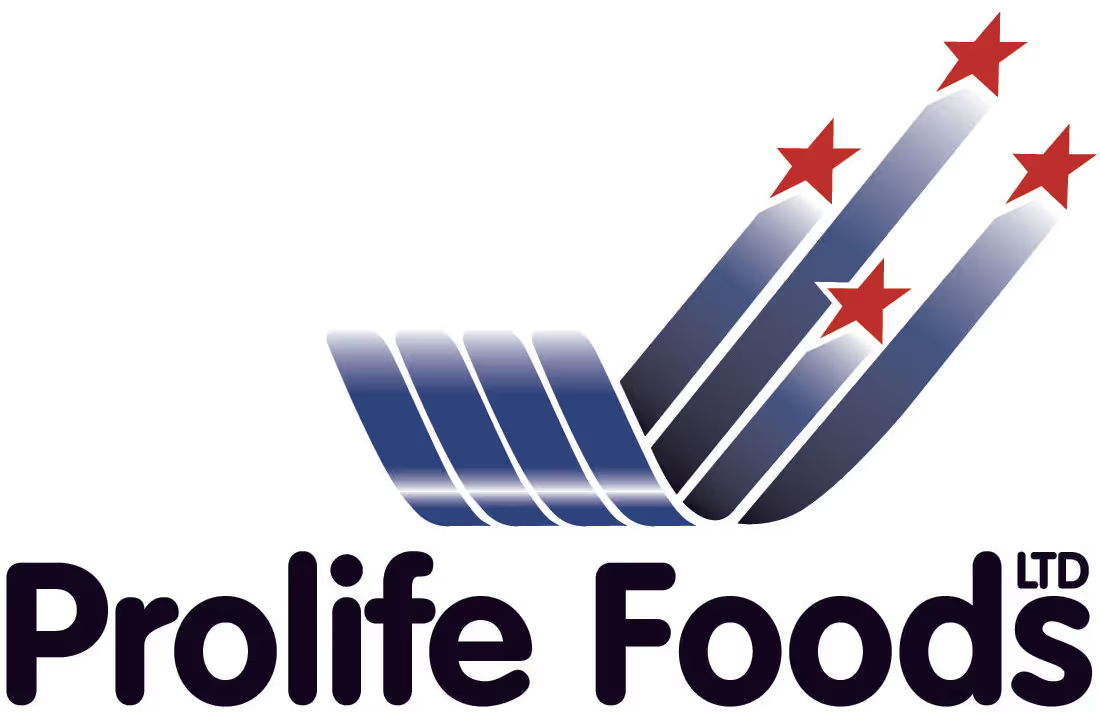
.png)
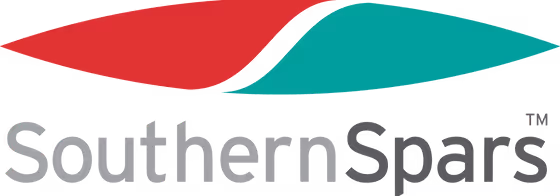
.svg.avif)

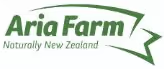
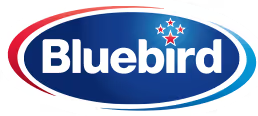
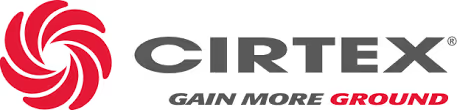

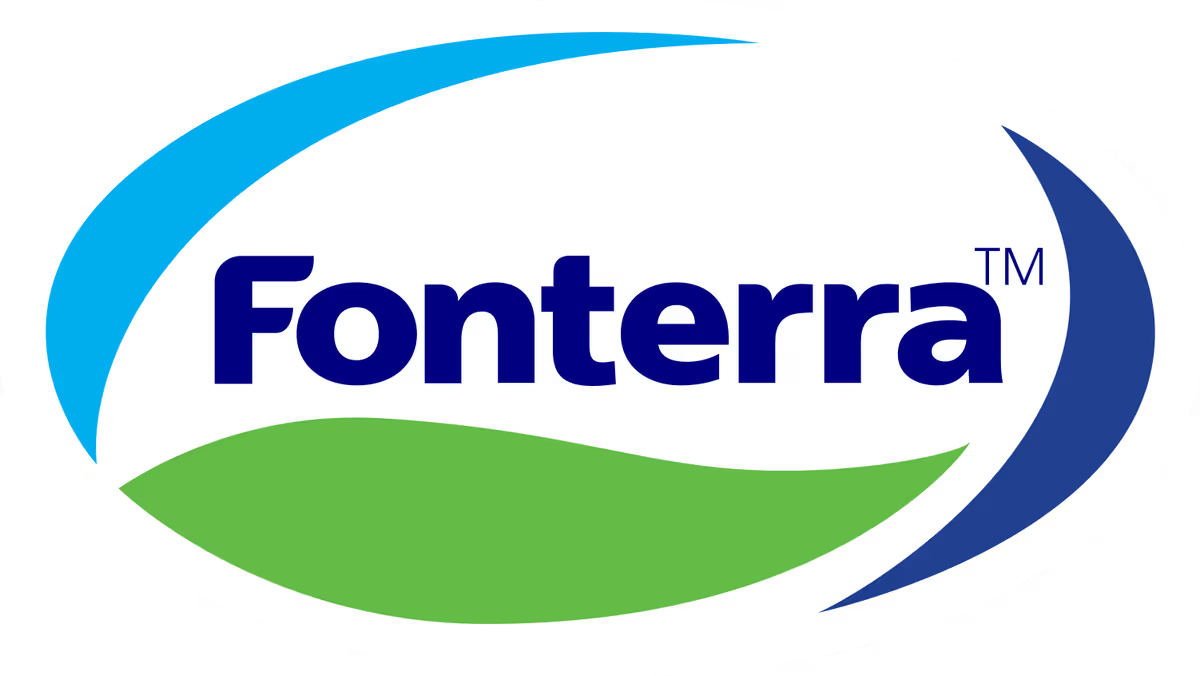
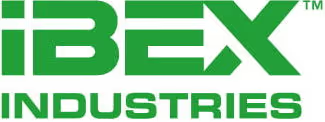
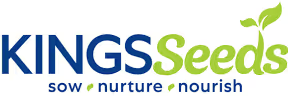
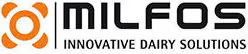
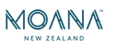
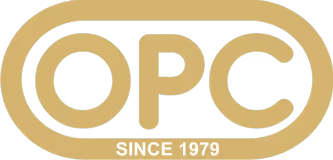
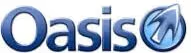
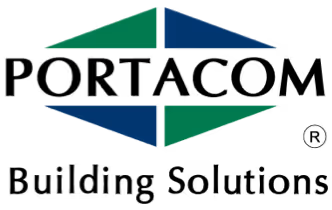
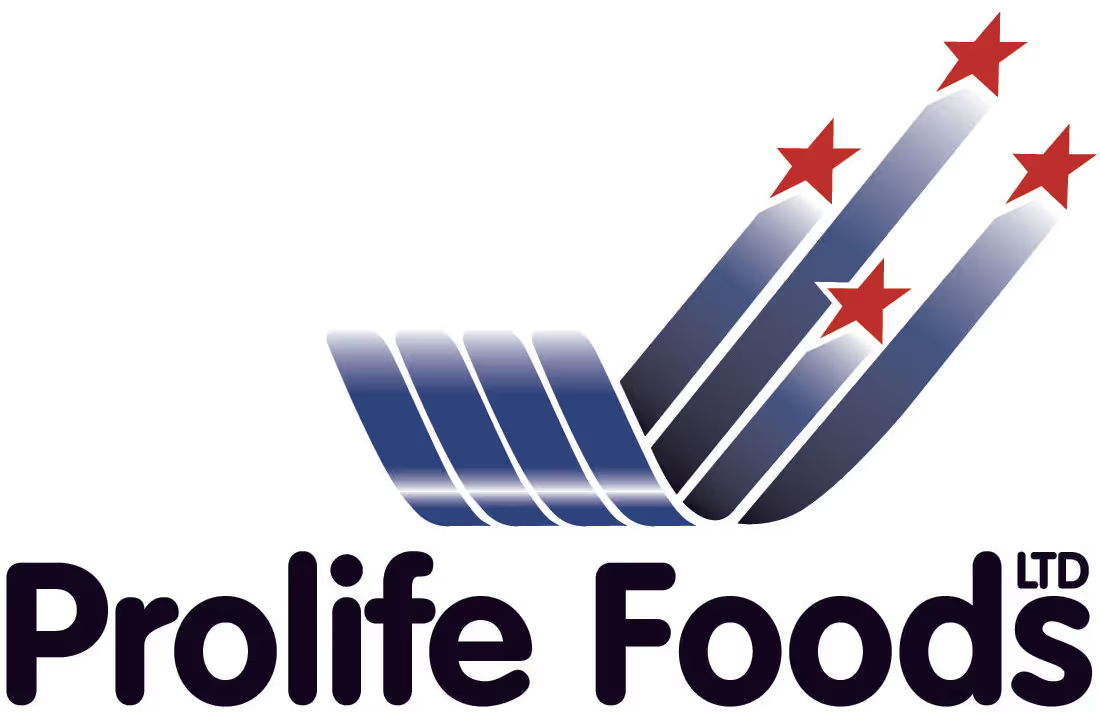
.png)
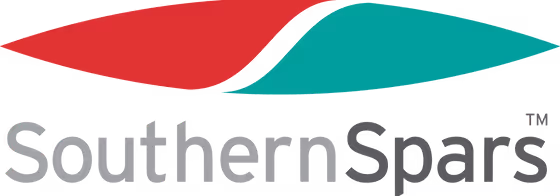
.svg.avif)
About Improvement Direct
Peter Maunder, Managing Director of Improvement Direct
Improvement Direct continues to develop and refine Lean Training and Consulting plans to support customers and draws on 20 years of business continuity in the challenging New Zealand Lean market. General Manager Peter Maunder will be your trainer and consultant. His most relevant training and experience comes from 15 years with Toyota. Through this time, Peter worked in Production, Quality Assurance and Education & Training applying, and fully understanding the Toyota Production System.
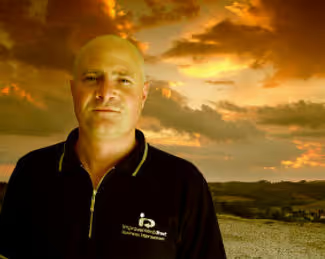
How Dominion Salt achieved 20% productivity Gains and annual savings of 200k!

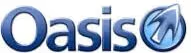
Thanks for your help over the last six months we have achieved, among other things:
A 30% reduction in set up times, A 50% reduction in assembly times.
A significantly improved meeting structure.
The improvement in communication throughout the company has been amazing.
Operations Manager

Peter from Improvement Direct has been working with us for 4 years. While we didn’t have catastrophic failures we did realise we needed help to de-risk the things we could control.
Peter's first 12 months focused on implementing a Sales & Operations Planning structure. Before we implemented S&OP failure was no surprise, Failure is now rare and now we can see what has happened and what we need to do to stop recurrence. The S&OP processes are simple, robust and work. Customer satisfaction, as reassured by our NPS tracking, has improved by 28% in the past 3 years.
We then started a full Lean Implementation plan following Improvement Directs Worxsmart tm Improvement Program. Peter has trained all employees in Lean / Worxsmart tools and has assisted with a wide range of improvement projects in all areas of the business. Worxsmart is now part of what we do and removes +$250,000 of waste every year. I recommend you give Peter a call if your systemic, sustainable improvement.
Brett Hobson
.png)
We at Puma Darts started our Lean journey almost 4 years ago, and at the time engaged Peter Maunder at Improvement Direct as our consultant to get us on the way... Whilst Peter was hands-on in getting things done, he was also hands-off enough to steer us and guide us in the right direction and let us find our own path as well. I believe that is one of the key things with Lean with Improvement Direct. It is very much 'your' project, they are just there to train and guide and assist on the journey.
The results we have had through Lean cannot be understated. A huge improvement in not only the factory tidiness, organisation, layout and the practicalities of the Lean journey. Team morale, and company culture have made huge improvements and really brought us all together as a team. For me, I think a big part of Lean journey is getting the involvement and commitment from staff buy-in from the start and get everybody working together.
As a result of that, and from the improvement ideas, set-ups, and training, we have substantially reduced cost across all departments (in some cases labour per unit has halved); done almost a complete re-layout of the dart area; moved machines, people; changed processes, production lines. We have added not only to the efficiency of the operation, but also made things easier and more practical for our staff and also produced a better quality product.
Peter McCormick
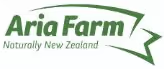
We have called our Lean program Aria Continuous Improvement.
ACI has revolutionized our business and the way we all think. Doing things a better and a more efficient way is what we are about all the time, it is a great culture to have and work in...
...I have learnt how to organise a lot better not only at work but also at home and everyday life.
Learning better and more efficient ways to setting up systems. Keeping area’s tidy and having a purpose for everything. Learning kanban, 5 s’s, quick change, idea mapping, personal development, scheduling etc. Lewis (Factory Manager)
Anna Arndt
